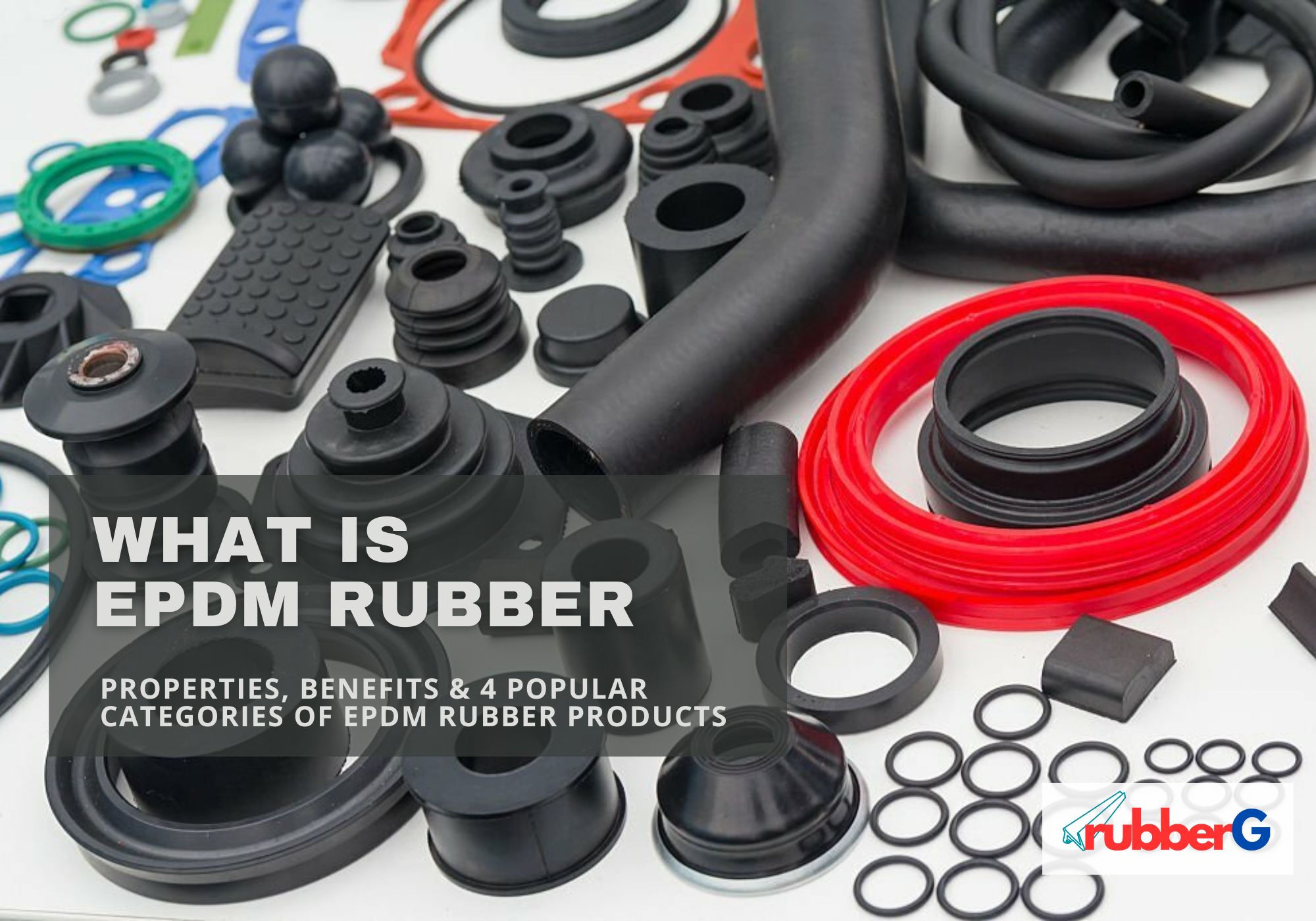
What is EPDM Rubber? Benefits & Popular Applications
Welcome to another definitive guide! Today, we will learn some fundamentals of EPDM rubber. It is a remarkable material used in a wide range of industries. Have you wondered how this revolutionized material came into this world? Let’s dive in and find out.
EPDM rubber typically came into popularity in the mid-20th century. At that time, scientists and engineers were on a quest to create high-quality rubber material. They wanted something that would be better than natural rubber. The aim was to create something that would offer more durability & ability to withstand harsh environments. They combined ethylene, propylene, and diene monomers during the experiment and gave birth to EPDM. It is now the world’s most popular rubber material used everywhere.
Therefore, we must recognize the importance of EPDM rubber. You may find this material in many applications, from roofing to automotive components. EPDM is also popular in HVAC systems and industrial equipment. So, this article aims to provide a comprehensive guide on rubber fundamentals. It begins with highlighting some advantages & disadvantages. Later, we will learn more about their wide applications. Ultimately, we can understand how natural rubber differentiates from EPDM rubber.
Table of Contents
What is EPDM Rubber?
EPDM stands for Ethylene, Propylene, Diene Monomar. It is a synthetic rubber famous for it’s excellent performance in many applications. This elastomer’s unique chemical makeup sets it apart from other materials.
Let’s imagine the chemical structure of EPDM. We can find that ethylene contributes to the overall structure of EPDM. It acts as a backbone of the EPDM chain. On the other hand, propylene is a hydrocarbon compound. It contributes to the flexibility & stability of the EPDM polymer. So, we may often find EPDM in applications that require rubber to be pliable & elastic. Finally, the diene monomer provides excellent heat resistance and vulcanization capabilities. It also improves the strength and durability of the EPDM rubber.
Pros
We know that EPDM rubber is prevalent in many applications. Why is it so popular? Indeed, it provides a wide range of benefits to different uses. Let’s find out some of the critical advantages of EPDM Rubber.
- EPDM rubber is exceptionally durable. It can withstand prolonged exposure to harsh environments. An example? Consider extreme temperatures, UV radiation, ozone, and weathering.
- Since EPDM is durable, you may not require frequent replacements.
- EPDM is extremely popular for weather-resistant applications. We may all see it in our houses, vehicles, or offices. EPDM rubber can endure extreme heat, cold, rain, and sunlight. As a result, they are a popular choice for roofing, gaskets, and seals.
- EPDM rubber is also chemical resistant. However, it may be vulnerable to some aggressive chemicals.
- It is flexible & offers prolonged durability.
- EPDM rubber is an excellent electrical insulator. It is commonly helpful in electrical cables & wires.
Cons
Although EPDM rubber offers many benefits, it still has some limitations. Some disadvantages of EPDM rubber include:
- EPDM rubber has a specific temperature range between which it can work perfectly. The typical temperature ranges from -60°C to 120/200°C (-60°F to 250/300°F).
- This material may not be suitable for some aggressive chemicals. In addition, it is not highly resistant to oils, greases, and petroleum-based products.
Properties of EPDM Rubber
As said earlier, EPDM is a mixture of ethylene, propylene, and diene monomers. Let’s consider the structure of the EPDM Rubber. The ethylene content of EPDM rubber is around 45% – 75%. Ethylene provides structural integrity & stability to the EPDM material. Next, propylene constitutes 15% to 50% of the EPDM polymer by weight. It gives the flexibility to the structure. Finally, diene monomer is present at 3% to 9% in the EPDM composition. It makes EPDM resistant to temperatures and chemicals.
Note that the percentage of this material content depends on the specific formulation of EPDM rubber. You can adjust it as per your project requirements. Adjusting this content % allows you to optimize flexibility and heat & chemical resistance properties.
Mechanical Properties
Mechanical properties determine the physical properties of EPDM Rubber. These properties help determine your EPDM’s durability & stability for specific applications.
Mechanical Property | Typical Value |
Tensile Strength | 500 – 2500 PSI |
Elongation at Break | 100% – 300% |
Adhesion to Metal | Good to Excellent |
Hardness or Durometer Range | 30 – 90 Shore A |
Adhesion to Rigid materials | Good to Excellent |
Impact Resistance | Good to Resistance |
Thermal Properties
Thermal properties determine the temperature ranges that EPDM can withstand. It may include operating temperature, thermal example, and transition temperature. These thermal values are crucial in those applications where temperature variations are significant.
Thermal Property | Typical Value |
Co-efficient of Thermal Expansion, Linear | 160 µm/(m·K) |
Maximum Service Temperature | 302°F |
Minimum Service Temperature | -58°F |
Glass Transition Temperature | 129°F |
How is EPDM Rubber Made
The manufacturing process of EPDM Rubber typically involves the mixing of specific raw materials. Typical manufacturing begins with a selection of ingredients. And then, the polymerization process combines propylene with ethylene. Next, the process incorporates Diene Monomer with the polymerized mixture. Finally, the vulcanization & processing process finalizes the production process of EPDM rubber. However, we can make EPDM (Ethylene Propylene Diene Monomer) through three primary methods.
Slurry Process
In the slurry method, the polymerization usually occurs in a liquid form. Let’s think of it like making a smoothie with ingredients that don’t quite mix. In this case, ethylene, propylene, and the diene monomer are used. Then, the process mixes these ingredients in a solvent and applies a catalyst to kickstart the polymerization. The result is tiny particles of EPDM floating in the liquid.
Solution Process
The solution process is a bit like brewing tea. All three ingredients are dissolved in a solvent. And then, the process adds catalysts to start the polymerization. After the reaction, you’re left with a solution of EPDM in the solvent.
Gas Phase Process
In this process, all three materials are vaporized & introduced into a reactor. Inside, they react to form EPDM particles. It’s like creating clouds from water vapor. Later, the process collects these particles and recycles unreacted gases.
Wide Applications of EPDM Rubber Products
From the above, we learned that EPDM rubber provides a wide range of benefits. Due to these benefits, EPDM rubber products are widely popular in many industries. The use of EPDM products is mainly seen in the construction & automotive industries. Besides, in HVAC applications, EPDM rubber products are also widely popular. EPDM is also used for electrical insulation, cable sheathing, and grommets in the electrical industry.
However, EPDM products are also in huge demand in the industrial & manufacturing sectors. Industries like marine, medical, and aerospace also use various EPDM products. After all, let’s look at the type of EPDM rubber products. The following four categories are widely popular in the mentioned industries.
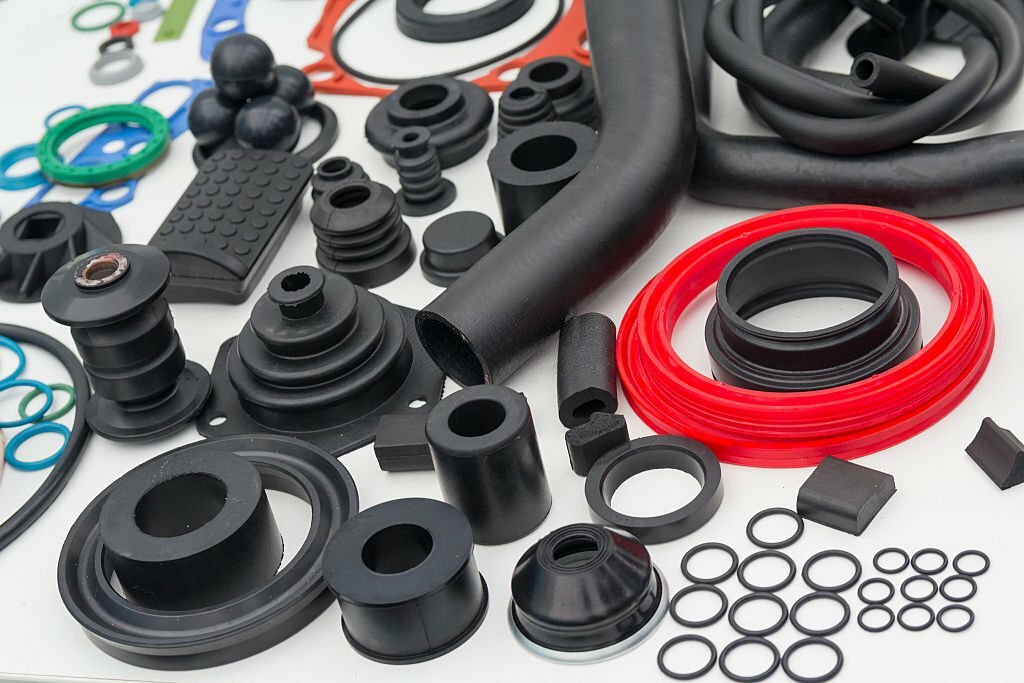
Rubber EPDM Roofing
- RV roofing: RV stands for Recreational Vehicles. RV roofing is the roofing system used in these vehicles.
- Roof membranes are a critical part of the roofing system. It provides a waterproof barrier. Note that this barrier protects the underlying structure from moisture & environmental elements.
- Roof Coatings are the protective surface of the roof. They enhance the roof’s performance & extend it’s lifespan.
HVAC Systems
- EPDM Rubber Seal Strips typically offer airtight connections within HVAC systems. It ensures efficient & controlled airflow.
- EPDM Gaskets and seals prevent leaks and maintain the integrity of HVSC components.
- Compressor grommets ensure quitter & more stable HVAC operation.
- Drain tubes prevent condensation-related issues.
Automotive
- EPDM Weatherstripping: The most popular use of an EPDM rubber strip is weatherstripping. It ensures a tight seal between car doors & windows. As a result, it offers a comfortable & protected interior from different elements.
- Door, window, and trunk seals are also crucial for preventing leaks. They provide sound insulation and contribute to a quitter & weather-resistant vehicle.
- Window spacers maintain the proper distance between glass panes. It enhances thermal insulation & structural integrity in automotive windows.
Industrial
- EPDM Oring & hose are prevalent for their resilience to environmental factors. They provide reliable seals and conduits in industrial machinery & systems.
- EPDM tubes and belts are famous for their flexibility. This makes them essential in conveying fluids and materials.
- Electrical insulator: EPDM elastomer is widely popular in insulating & protecting cables & wires.
- EPDM Rubber Cord: Industrial settings use an EPDM cord for sealing, insulation, and vibration damping.
Summary
Let’s wrap everything up! EPDM is a versatile synthetic rubber material. It’s wide range of benefits made EPDM famous in various industries. Throughout the article, we discussed EPDM rubber’s fundamentals and it’s products. We learned their properties, benefits, and limitations. All this information clearly differentiates EPDM rubber from natural rubber. We have justified that EPDM is superior to natural rubber. Although natural rubber is cheaper, it may not be suitable for a lot of applications.
Moreover, natural rubber is more elastic & flexible than EPDM. EPDM is also elastic but not as stretchy as natural rubber in this case. However, EPDM is the best for factors like resistance to various elements, applications, and durability. Please note that the properties of both natural EPDM & natural rubber may vary based on specific formulations.
Above all, if you have any questions concerning EPDM rubber, don’t hesitate to contact us. Our team of experts is eager to answer all your questions. So, that’s all for today. We hope this guide will help you clearly find the right product for your applications.